Three Roller Mill: A Key Tool in Precision Grinding and Dispersion
In industries ranging from cosmetics to electronics, achieving the right texture, consistency, and dispersion of materials is crucial. One of the most effective tools for this purpose is theThree Roller Mill. This piece of equipment is renowned for its ability to finely grind and disperse materials with high precision. In this blog, we'll explore what a three roller mill is, how it works, its applications, and the advantages it offers.
●What is a Three Roller Mill?
A three roller mill is a machine that uses three horizontally positioned rollers to grind, mix, refine, or disperse materials. The rollers are typically made of hard, wear-resistant materials like stainless steel, ceramic, or hardened carbon steel. The rollers rotate at different speeds, creating a shearing force that finely grinds the material as it passes through the gaps between them.
●How Does a Three Roller Mill Work?
The operation of a three roller mill involves the following steps:
1.Feeding: The material to be processed is fed into the gap between the first and second rollers, known as the feed nip.
2.Grinding and Shearing: As the rollers rotate, the material is drawn into the narrow gap between the first and second rollers. The pressure and shearing action between these rollers begin to break down and grind the material.
3.Further Refinement: The partially processed material then moves to the gap between the second and third rollers, where it undergoes further grinding and refinement. This second pass ensures that the material is ground to the desired fineness and that any remaining particles are fully dispersed.
4.Collection: The final product is collected from the third roller, ready for use in various applications.
●Applications of Three Roller Mills
Three roller mills are widely used in industries that require precise grinding and dispersion of materials. Some of the key applications include:
1.Cosmetics and Personal Care Products
In the cosmetics industry, three roller mills are used to create smooth and uniform dispersions of pigments, creams, and lotions. The fine grinding capability of the mill ensures that products have a consistent texture and appearance, which is critical for high-quality cosmetics.
2.Printing Inks
The production of printing inks requires the dispersion of pigments in a liquid medium. Three roller mills are ideal for this process, as they can achieve the fine particle size and uniform distribution needed for high-quality printing inks, ensuring vibrant colors and consistent print quality.
3.Paints and Coatings
In the paints and coatings industry, achieving a smooth and uniform finish is essential. Three roller mills are used to grind pigments and other materials into fine particles, ensuring that the final product has the desired consistency and color uniformity.
4.Adhesives and Sealants
The precise grinding and mixing capabilities of three roller mills make them suitable for the production of adhesives and sealants. These materials often require a fine and homogenous mixture to ensure strong bonding and reliable performance.
5.Electronics
In the electronics industry, three roller mills are used to process conductive and insulating materials for various applications, including the production of printed circuit boards (PCBs) and electronic components. The mill's ability to achieve fine and uniform dispersion is crucial for ensuring the performance and reliability of electronic devices.
●Advantages of Using a Three Roller Mill
1.Precision Grinding: Three roller mills offer unparalleled precision in grinding and dispersion, making them ideal for applications that require high-quality, fine particle distributions.
2.Consistency and Uniformity: The controlled shearing action of the rollers ensures that materials are processed evenly, resulting in consistent and uniform end products.
3.Versatility: Three roller mills can be used for a wide range of materials, from pastes and creams to solids and liquids, making them versatile tools in many industries.
4.Scalability: These mills are available in various sizes, allowing for scalability from laboratory testing to full-scale production.
5.Efficiency: The design of the three roller mill allows for efficient processing with minimal waste, making it a cost-effective solution for many applications.
●Factors to Consider When Choosing a Three Roller Mill
When selecting a three roller mill, several factors should be considered to ensure it meets the specific needs of the application:
1.Roller Material: The material of the rollers should be chosen based on the abrasiveness and hardness of the materials being processed. Common options include stainless steel, ceramic, and carbon steel.
2.Gap Adjustment: The ability to adjust the gaps between the rollers is crucial for controlling the fineness of the grind and ensuring consistent results.
3.Roller Speed: The speed at which the rollers rotate can affect the grinding and dispersion process. Some mills allow for adjustable speeds to accommodate different materials and processing requirements.
4.Capacity: The size and capacity of the mill should be matched to the production needs, whether for small-scale laboratory work or large-scale manufacturing.
5.Ease of Cleaning: For applications where cross-contamination must be avoided, it's important to choose a mill that is easy to clean and maintain.
●Conclusion
The three roller mill is a powerful and versatile tool that plays a vital role in many industries. Its ability to precisely grind and disperse materials makes it indispensable for the production of high-quality products, from cosmetics and inks to paints and electronics. By understanding the functions, applications, and advantages of three roller mills, manufacturers can make informed decisions to enhance their production processes and achieve superior results.
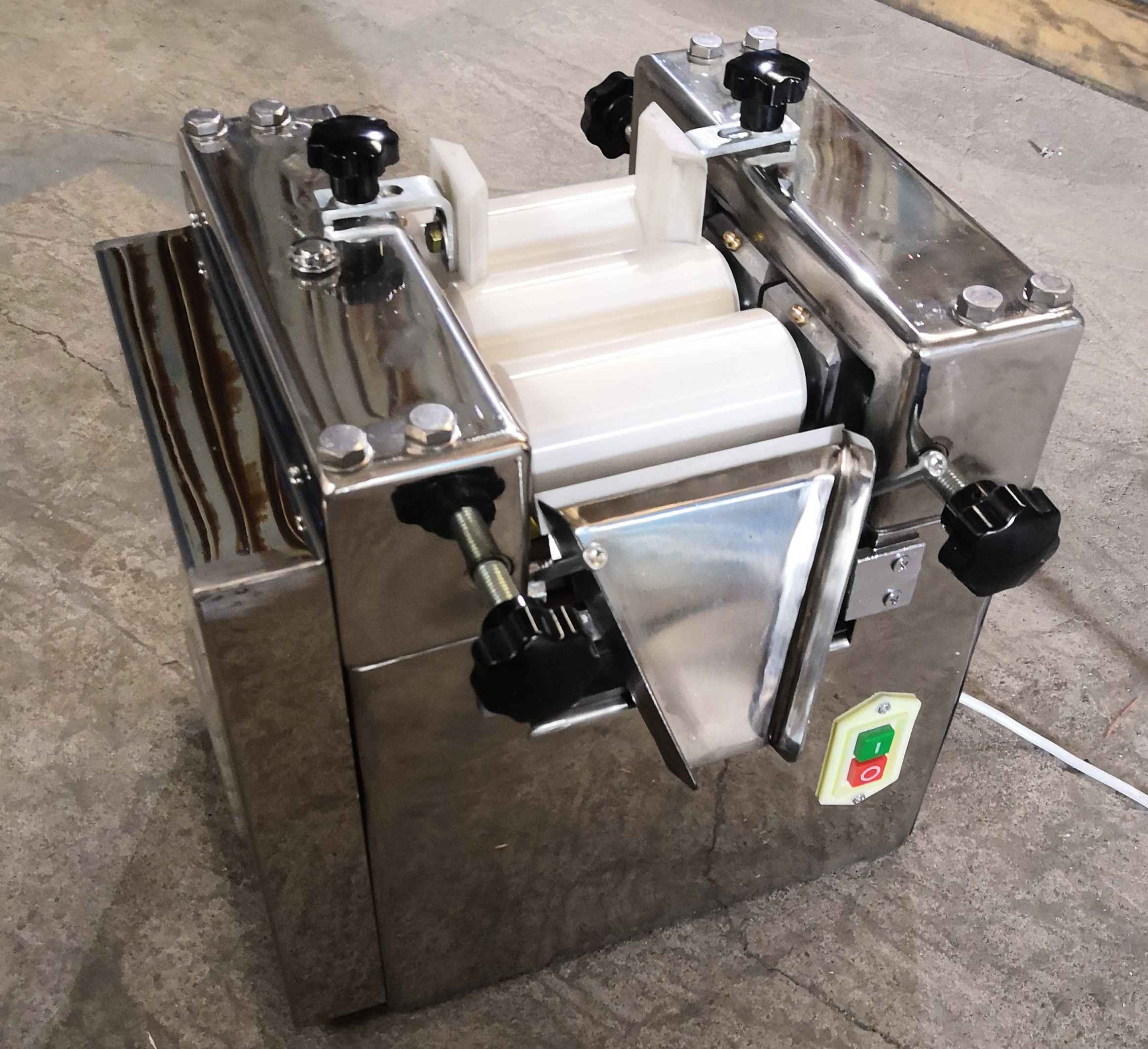