Lithium Cell Manufacturing Line: A Comprehensive Overview
A lithium cell manufacturing line is a highly specialized production system designed to assemble lithium-ion batteries, which are essential for a variety of applications such as electric vehicles (EVs), consumer electronics, renewable energy storage, and more. These production lines are crucial for scaling up battery manufacturing, ensuring consistency, performance, and quality control in every cell produced.
Lithium-ion batteries are favored for their high energy density, long life cycle, and relatively low weight, making them ideal for portable electronics and electric vehicles. As demand for these batteries increases, especially with the growth of the electric vehicle market, the need for efficient, automated manufacturing lines becomes more critical.
---
Key Steps in the Lithium Cell Manufacturing Process
1. Electrode Preparation
- Slurry Mixing: The process begins with mixing active materials (such as lithium cobalt oxide or lithium iron phosphate), binders, and solvents to create a slurry.
- Coating: The slurry is coated onto metal foils (typically aluminum for the cathode and copper for the anode). This step is crucial to ensure a uniform distribution of the active material.
- Drying: After coating, the electrodes are dried in an oven to remove the solvents and ensure that the coating is solid and adheres well to the metal foils.
- Calendaring: The dried electrodes are passed through a calendaring machine to compress them to a specific thickness and improve their density.
2. Electrode Cutting
- The electrodes are cut to precise sizes, ready for assembly into the battery cell. This includes cutting both the cathode and anode materials to fit into the cell design.
3. Cell Assembly
- Stacking or Winding: In this step, the anode, cathode, and separator are assembled together. The most common configuration is the "jelly roll" method (for cylindrical cells), where the anode, cathode, and separator are rolled up into a spiral shape. For pouch cells, the electrodes are stacked in layers.
- Tab Welding: The electrodes are connected to tabs, which will be used to establish the electrical connections once the cell is fully assembled.
4. Electrolyte Filling
- After the assembly, the cells are filled with an electrolyte solution. The electrolyte is essential for facilitating the movement of ions between the anode and cathode during charging and discharging.
5. Cell Sealing
- After electrolyte filling, the cell is sealed in a casing, which is typically made of metal or plastic. The sealing process must ensure that the cell is airtight and safe from external environmental factors.
6. Formation Process
- Initial Charging/Discharging: The cell undergoes an initial charge and discharge cycle, known as the formation process. This step activates the cell's chemistry and ensures that the battery is functioning correctly.
- Aging: The cell is stored in controlled conditions for a certain period to stabilize the electrolyte and allow the battery's performance to stabilize.
7. Testing and Quality Control
- The cell undergoes a series of tests to ensure it meets the required specifications. These tests may include:
- Capacity testing: Ensuring the cell provides the rated power.
- Cycle life testing: Assessing the battery’s longevity.
- Safety tests: Ensuring the cell can withstand overcharging, short circuits, and other potentially hazardous conditions.
8. Packaging and Final Inspection
- Once the cell passes all tests, it is packaged and labeled according to customer specifications. Final inspections check for external damage and ensure the battery is fully operational.
---
Key Components of a Lithium-ion Pouch Cell Production
1. Electrode Coating Line
- Coating Machines: These machines are responsible for applying the slurry onto the metal foils evenly.
- Drying Ovens: Drying ovens remove the solvent and solidify the coating.
- Calendaring Machines: Compress the coated electrodes to the desired thickness.
2. Electrode Cutting and Assembly Line
- Electrode Cutting Machines: Ensure precise cutting of the electrodes to the required sizes.
- Tab Welding Machines: These machines weld the tabs to the electrodes to ensure electrical contact.
3. Cell Assembly Equipment
- Winding and Stacking Machines: Depending on the cell type (cylindrical or pouch), this equipment is used to assemble the electrodes into the final configuration.
- Electrolyte Filling Equipment: Injects the electrolyte into the cell in a controlled manner.
- Sealing Machines: Seals the cell casing, ensuring it is airtight and stable.
4. Formation and Testing Equipment
- Formation Equipment: Performs the first charge and discharge cycle to activate the cell.
- Battery Testing Equipment: Tests the battery's performance, including charge capacity, internal resistance, and cycle life.
- Aging Chambers: Stores cells under controlled temperature and humidity to ensure stability.
---
Advantages of a Fully Integrated Lithium Cell Manufacturing Line
1. High Efficiency
- Automation in every step of the manufacturing process allows for faster production times and reduced labor costs. Automation also ensures consistency, reducing human error and enhancing overall efficiency.
2. Scalability
- Modern manufacturing lines can be scaled up or down based on demand. Newer machines and equipment allow for mass production without compromising on quality.
3. Precision and Quality Control
- The precision of modern equipment ensures that every aspect of the cell, from electrode coating to sealing, is performed with high accuracy. Stringent testing processes help guarantee product quality and safety.
4. Cost-Effectiveness
- With large-scale production, the cost per unit decreases significantly, making the production of lithium-ion batteries more cost-effective. Efficient use of materials and reduction of waste also contributes to lowering production costs.
5. Flexibility
- Modern lithium cell manufacturing lines can accommodate different sizes and chemistries of batteries, offering flexibility for manufacturers to cater to various market needs.
---
Challenges in Lithium Cell Manufacturing
1. Material Supply Chain
- Lithium-ion battery manufacturing relies on specific raw materials, such as lithium, cobalt, nickel, and graphite. The availability and price fluctuations of these materials can impact the manufacturing process.
2. High Initial Investment
- Establishing a lithium cell manufacturing line requires a significant upfront investment in equipment and facilities. This is particularly true for high-throughput production lines that require advanced automation and precision machinery.
3. Environmental Concerns
- The production of lithium-ion batteries can generate waste, and the disposal of these batteries, particularly at the end of their life cycle, poses environmental challenges. Manufacturers need to ensure that they have sustainable practices in place, including recycling and minimizing hazardous by-products.
4. Battery Safety
- As batteries increase in size and energy density (especially in EVs), ensuring the safety of the cells during manufacturing and operation becomes even more critical. Any manufacturing defect, such as impurities or incorrect sealing, can lead to safety issues like thermal runaway, fires, or explosions.
---
Conclusion
A lithium cell manufacturing line is a sophisticated system designed to produce high-quality lithium-ion batteries efficiently and safely. It integrates advanced machinery and automation to handle every step of the production process, from electrode preparation to final testing. With the growing demand for lithium-ion batteries in sectors like electric vehicles and renewable energy storage, establishing a reliable and scalable manufacturing line is crucial for meeting both market needs and safety standards. As technology continues to evolve, improvements in production lines will enable the industry to meet the rising demand for high-performance, cost-effective batteries.
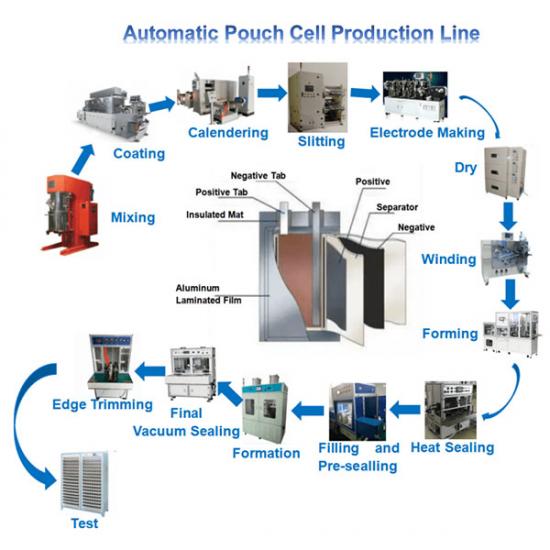